Affiliate Disclosure
HVAC Guide Guys is a participant in the Amazon Services LLC Associates Program, an affiliate advertising program designed to provide a means for sites to earn advertising fees by advertising and linking to Amazon.
How Do Oil Burner Nozzles Work HVAC? This component ensures the proper mixture of air and oil for optimal heating performance. By controlling the nozzle size and shape, the burner can adjust the amount of fuel delivered, affecting the system’s efficiency and heat output. Understanding how oil burner nozzles operate is essential for maintaining a well-functioning heating system and maximizing energy efficiency.
Oil burner nozzles work by atomizing oil into a fine mist for combustion in HVAC systems. The nozzle’s spray pattern and flow rate are crucial for efficient fuel combustion.
Proper maintenance and occasional replacement of the nozzle are necessary to ensure consistent and reliable operation in HVAC applications.
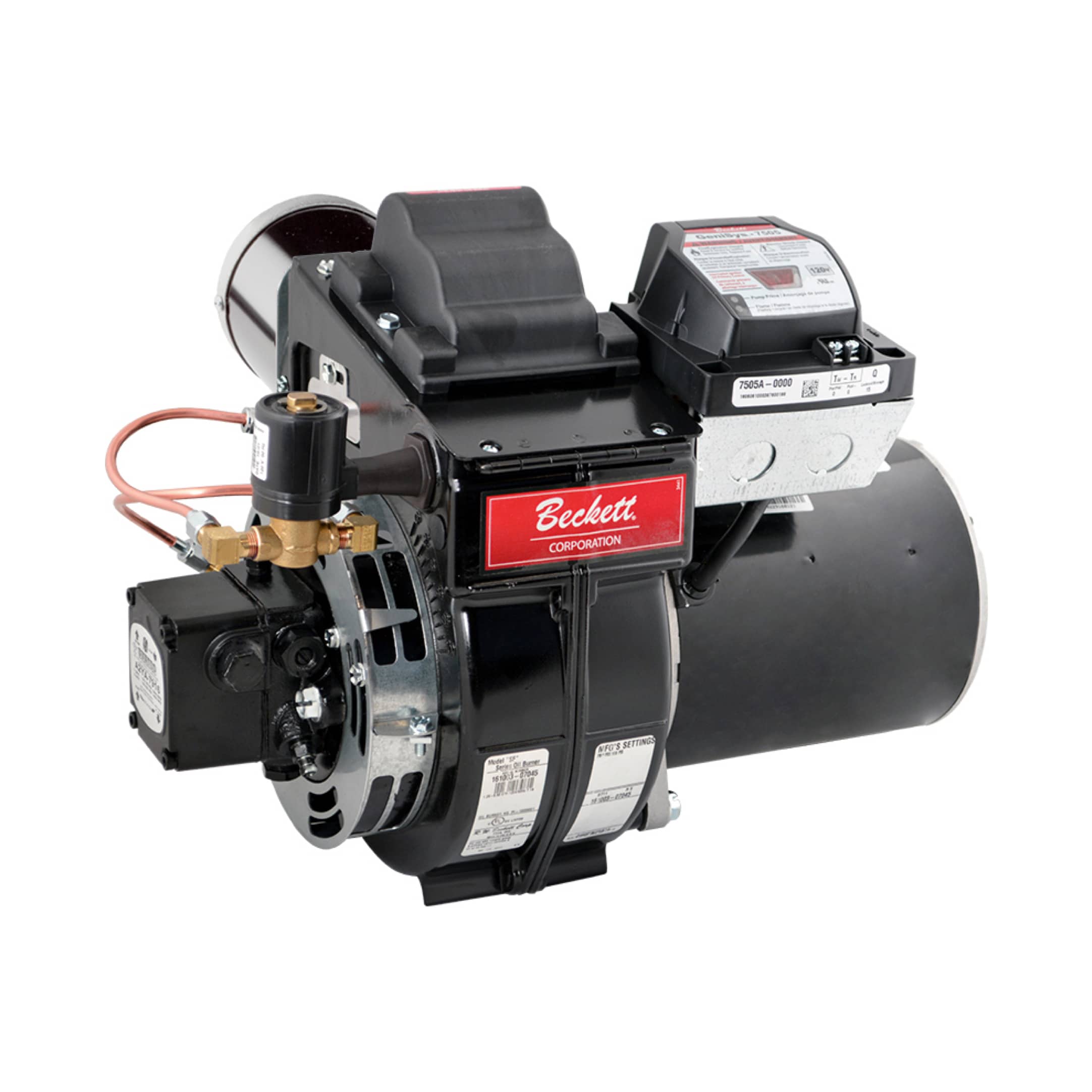
Credit: www.beckettcorp.com
Table of Contents
Introduction To Oil Burner Nozzles
Oil burner nozzles in HVAC systems work by atomizing fuel into a fine mist for efficient combustion, ensuring optimal heat output. The nozzle’s spray pattern and size play a crucial role in controlling the fuel-air mixture, impacting the burner’s performance and energy efficiency.
Explore Our HVAC Shop
Looking for top-rated HVAC tools, parts, and accessories? Visit our shop and find the perfect solution for your needs.
Visit the ShopPurpose In HVAC Systems
Oil burner nozzles play a crucial role in the efficient functioning of HVAC systems. These nozzles are responsible for delivering a precise mixture of fuel and air into the combustion chamber. By controlling the flow rate, spray pattern, and droplet size, oil burner nozzles ensure optimal combustion, resulting in efficient heat generation and reduced emissions.
Types Of Oil Burner Nozzles
Oil burner nozzles come in different types, each designed to meet specific requirements in HVAC systems. Here are some common types of oil burner nozzles:
- Hollow Cone Nozzles: These nozzles produce a hollow cone-shaped spray pattern, ideal for applications where a high degree of atomization is needed. They provide efficient fuel combustion and are commonly used in residential and commercial heating systems.
- Solid Cone Nozzles: Solid cone nozzles create a solid cone-shaped spray pattern, making them suitable for applications that require a more focused and concentrated flame. They are commonly used in industrial heating systems.
- Semi-Solid Cone Nozzles: These nozzles combine the characteristics of both hollow cone and solid cone nozzles. They produce a partially hollow spray pattern and are often used in medium-sized combustion systems.
- Full Cone Nozzles: Full cone nozzles produce a full cone-shaped spray pattern, dispersing the fuel evenly in all directions. They are commonly used in large-scale industrial heating systems.
- Variable Flow Nozzles: As the name suggests, variable flow nozzles allow for adjustable fuel flow rates. They offer flexibility in controlling the heat output of the burner, making them suitable for applications where the heat demand varies.
In conclusion, oil burner nozzles play a vital role in HVAC systems by ensuring efficient combustion and heat generation. Understanding the purpose and different types of oil burner nozzles can help in selecting the right nozzle for specific heating requirements.
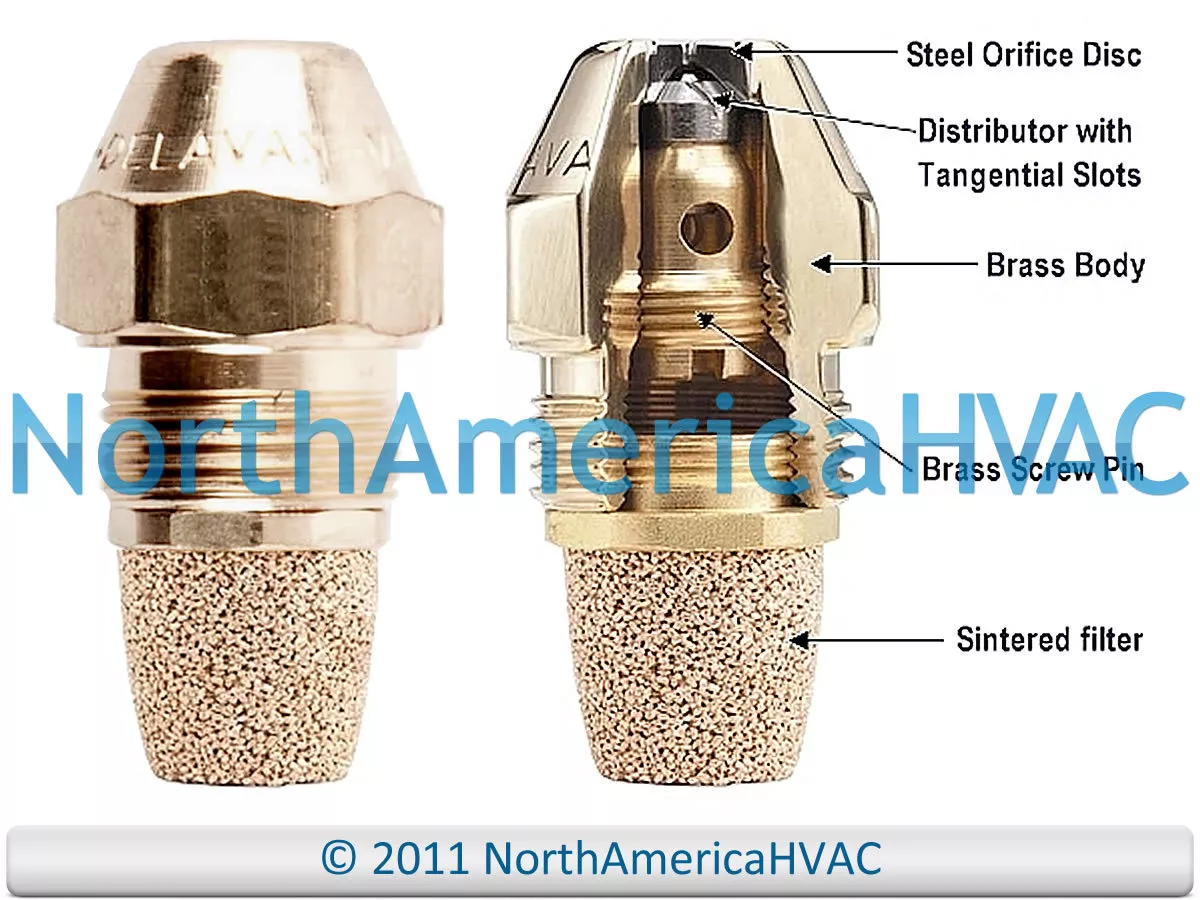
Credit: www.ebay.com
Explore Our HVAC Shop
Looking for top-rated HVAC tools, parts, and accessories? Visit our shop and find the perfect solution for your needs.
Visit the ShopDesign And Construction
Oil burner nozzles in HVAC systems work by delivering a precise mixture of fuel and air to create a flame. The nozzle’s design and construction play a crucial role in regulating the flow and spray pattern of the oil, ensuring efficient combustion and optimal heating performance.
Design and Construction are crucial factors in understanding how oil burner nozzles work in HVAC systems. The nozzle is responsible for atomizing the fuel oil into a fine mist, which is then ignited to produce heat. The design and construction of the nozzle play a critical role in ensuring that the fuel is atomized correctly, and the combustion process is efficient. In this section, we will explore the Material Composition and Nozzle Anatomy of oil burner nozzles.
Material Composition
Oil burner nozzles are typically made of brass, stainless steel, or hardened steel. The material composition is crucial in ensuring the nozzle’s durability and resistance to wear and tear caused by the high-velocity fuel oil flow. Brass is the most common material used for nozzles due to its excellent corrosion resistance and ease of machining. Stainless steel is another popular choice due to its superior strength and resistance to high-temperature corrosion. Hardened steel is the most durable of all materials and is used in nozzles that are exposed to harsh operating conditions.
Nozzle Anatomy
The anatomy of an oil burner nozzle comprises several critical components that work together to deliver the fuel oil in a fine mist. The nozzle consists of a body, cap, filter, and spray plate. The body of the nozzle houses the orifice, which is responsible for controlling the fuel flow rate. The cap fits over the body and holds the filter and spray plate in place. The filter prevents any impurities from entering the nozzle and clogging the orifice, while the spray plate is responsible for atomizing the fuel oil. The spray plate has several holes that create a fine mist of fuel oil, which is then ignited to produce heat.
In summary, the design and construction of oil burner nozzles play a crucial role in ensuring efficient combustion and heating in HVAC systems. The material composition and nozzle anatomy are critical factors that determine the nozzle’s durability, resistance to wear and tear, and ability to atomize the fuel oil correctly.
Fuel Atomization Process
The fuel atomization process is a critical component of oil burner nozzles, playing a key role in the efficient and effective combustion of fuel. This process involves breaking down the fuel into tiny droplets to ensure proper mixing with air, ultimately leading to optimal combustion within the HVAC system.
Breaking Down The Science
Oil burner nozzles utilize the fuel atomization process to finely disperse the fuel into a mist of tiny droplets. This is achieved through the use of a nozzle, which is designed to create a high-velocity spray pattern, effectively breaking down the fuel into smaller particles for improved combustion.
Impact On Combustion
The fuel atomization process has a direct impact on combustion within the HVAC system. By creating a fine mist of fuel droplets, the process ensures thorough mixing with air, promoting efficient and clean combustion. This results in improved energy efficiency and reduced emissions, contributing to the overall performance and environmental friendliness of the oil burner nozzle.
Nozzle Sizing And Selection
When it comes to oil burner nozzles, proper sizing and selection are crucial for optimal performance and efficiency. The size of the nozzle determines the amount of fuel that is delivered to the burner, and it must be chosen carefully to match the specific requirements of the system.
Determining The Correct Size
Determining the correct size of the oil burner nozzle involves considering factors such as the heat output required, the furnace or boiler design, and the type of fuel being used. The size of the nozzle is typically measured in gallons per hour (GPH), indicating the flow rate of fuel. By selecting the appropriate GPH rating, the nozzle can deliver the right amount of fuel to achieve the desired heat output.
Several methods can be used to determine the correct nozzle size. One common approach is to consult the manufacturer’s specifications or guidelines for the specific burner model. These guidelines often provide recommendations based on factors like the furnace or boiler size and the desired firing rate. Additionally, HVAC professionals can rely on their experience and expertise to accurately determine the correct nozzle size based on the unique requirements of each system.
Adapting To Burner Requirements
Oil burner systems can have different requirements depending on factors such as the type of burner, the combustion chamber design, and the fuel pressure. It is essential to ensure that the selected nozzle is compatible with these requirements to achieve optimal performance.
For example, some burners may require a specific spray angle or pattern for efficient combustion. In such cases, selecting a nozzle that provides the desired spray characteristics is crucial. Manufacturers often provide guidance on the suitable nozzle types for their burners, taking into account factors like the atomization method and the burner’s air-to-fuel ratio requirements.
Another consideration is the fuel pressure. Different nozzles are designed to operate at specific pressure ranges, and it is important to choose a nozzle that matches the pressure of the burner system. This ensures proper atomization of the fuel and prevents issues like incomplete combustion or excessive sooting.
By carefully sizing and selecting the oil burner nozzle, HVAC professionals can optimize the performance and efficiency of the system. The correct nozzle size and type, adapted to the specific requirements of the burner, contribute to reliable operation, reduced fuel consumption, and minimized emissions.
Explore Our HVAC Shop
Looking for top-rated HVAC tools, parts, and accessories? Visit our shop and find the perfect solution for your needs.
Visit the ShopSpray Patterns And Their Significance
Oil burner nozzles in HVAC systems work by using different spray patterns to distribute fuel efficiently. These spray patterns, such as hollow, solid, or semi-solid, have significant effects on combustion, atomization, and flame shape. Understanding the significance of spray patterns is crucial for optimizing the performance of oil burner nozzles in HVAC systems.
Pattern Types
An oil burner nozzle is a crucial component of an HVAC system, responsible for atomizing fuel oil into a fine spray for efficient combustion. The spray pattern produced by the nozzle plays a significant role in the overall performance and efficiency of the burner. There are different types of spray patterns that vary in shape and angle, each with its own significance.
Let’s take a closer look at the various pattern types:
- Hollow Cone: This spray pattern forms a hollow cone shape, with a ring of fuel droplets around the outer edge. It is commonly used in applications where a more focused and directed flame is required. The hollow cone pattern is ideal for burners that operate at higher firing rates and require precise control over the flame shape.
- Solid Cone: Unlike the hollow cone pattern, the solid cone pattern produces a continuous cone shape without any gaps. It provides a more uniform distribution of fuel droplets, resulting in a broader flame pattern. Solid cone nozzles are commonly used in residential heating systems where a wider coverage area is required.
- Flat Fan: As the name suggests, the flat fan pattern produces a flat, fan-shaped spray. It is often used in industrial applications where a wide, thin flame is needed to cover a large surface area. Flat fan nozzles are also commonly used in spray drying processes and cooling applications.
Choosing The Right Pattern
When it comes to selecting the right spray pattern for an oil burner nozzle, several factors need to be considered:
- Firing Rate: The firing rate of the burner determines the amount of fuel that needs to be atomized. Higher firing rates often require a more focused and directed spray pattern to ensure efficient combustion.
- Combustion Chamber Design: The design of the combustion chamber can influence the airflow and flame characteristics. Choosing a spray pattern that complements the chamber design can optimize the burner’s performance.
- Application: Different applications may have specific requirements in terms of flame shape, coverage area, and heat distribution. Understanding the specific needs of the application is crucial in selecting the appropriate spray pattern.
By considering these factors, HVAC professionals can choose the right spray pattern that maximizes fuel efficiency, enhances combustion, and ensures optimal performance of the oil burner nozzle.
Maintaining Peak Efficiency
Oil burner nozzles play a crucial role in maintaining peak efficiency for HVAC systems. By carefully controlling the flow and atomization of fuel, these nozzles ensure optimal combustion, minimizing energy waste and maximizing performance. Understanding how oil burner nozzles work is essential for maintaining HVAC efficiency.
Regular Cleaning
Regular cleaning of oil burner nozzles is crucial for maintaining peak efficiency. Clean nozzles ensure proper fuel atomization and combustion, leading to optimal heat transfer and energy efficiency. Over time, soot, dirt, and debris can accumulate in the nozzle, affecting its performance. Therefore, it is important to schedule routine cleanings to prevent clogs and ensure consistent, efficient operation.
Timely Replacement
Timely replacement of oil burner nozzles is essential for sustaining peak efficiency. Worn-out nozzles can lead to improper fuel distribution and inefficient combustion, resulting in reduced heating performance and increased energy consumption. By replacing nozzles at recommended intervals, HVAC systems can continue to operate at their optimal level, providing reliable and cost-effective heating solutions.
In conclusion, maintaining peak efficiency in oil burner nozzles requires regular cleaning and timely replacement. By adhering to these practices, HVAC systems can deliver consistent and efficient performance, contributing to energy savings and long-term reliability.
Common Issues And Troubleshooting
Oil burner nozzles play a crucial role in HVAC systems by atomizing fuel for combustion. Common issues with oil burner nozzles include clogging and wear, leading to improper fuel delivery and inefficient burning. Troubleshooting involves cleaning or replacing the nozzle to ensure optimal performance and energy efficiency for the HVAC system.
Clogs And Blockages
Oil burner nozzles can get clogged with debris affecting performance.
Wear And Tear
Regular use can lead to wear and tear on the nozzle components.
Advancements In Nozzle Technology
Advancements in nozzle technology have revolutionized the way oil burner nozzles operate, offering increased efficiency and performance in HVAC systems.
Innovations For Enhanced Efficiency
New nozzle designs improve fuel atomization, enhancing combustion efficiency.
- Smaller droplet sizes result in more complete fuel burning.
- Precision engineering allows for better control over fuel flow rates.
- Variable nozzle patterns cater to specific heating demands.
Future Trends
Technological advancements point towards further nozzle enhancements.
- Integration of AI for real-time nozzle adjustments.
- Development of eco-friendly nozzles for sustainable heating solutions.
- Enhanced durability and longevity for extended nozzle lifespan.
Environmental Impact And Regulations
When discussing oil burner nozzles in HVAC systems, it’s crucial to consider their environmental impact and the regulations surrounding their use.
Emission Standards
Oil burner nozzles must meet strict emission standards to minimize pollution and protect the environment.
Eco-friendly Design Considerations
Implementing eco-friendly design elements in oil burner nozzles helps reduce carbon footprint and promote sustainability.
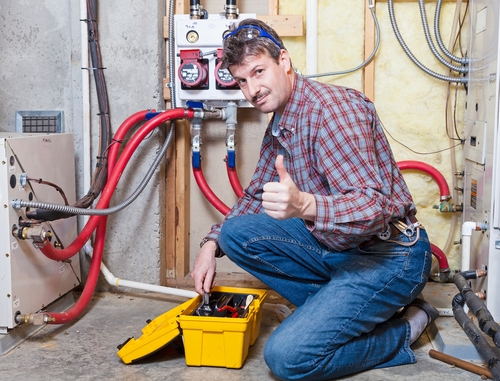
Credit: www.griffithenergyservices.com
Explore Our HVAC Shop
Looking for top-rated HVAC tools, parts, and accessories? Visit our shop and find the perfect solution for your needs.
Visit the ShopFrequently Asked Questions
How Does An Oil Burner Nozzle Work?
The nozzle functions by atomizing fuel oil into fine droplets and spraying it into the combustion chamber. The spray pattern and size of the droplets are determined by the nozzle’s design. The nozzle is also responsible for controlling the amount of fuel that enters the combustion chamber, ensuring that the furnace operates at maximum efficiency.
How Often Should Oil Burner Nozzles Be Replaced?
Oil burner nozzles should be replaced annually as part of routine maintenance. Over time, nozzles can become clogged or worn, resulting in decreased efficiency and increased fuel consumption. Replacing the nozzle ensures that the furnace operates at maximum efficiency.
What Is The Best Nozzle Size For An Oil Burner?
The best nozzle size for an oil burner is dependent on the furnace’s specifications. It is critical to choose the right size nozzle to ensure that the furnace operates at maximum efficiency. A nozzle that is too small will result in incomplete combustion, while a nozzle that is too large will waste fuel and increase emissions.
How Can I Tell If My Oil Burner Nozzle Is Clogged?
A clogged oil burner nozzle can cause a range of problems, including poor combustion, decreased efficiency, and increased fuel consumption. If you notice sooty deposits around the burner or a yellow flame, it may be an indication that the nozzle is clogged.
A professional HVAC technician should be contacted to diagnose and resolve the issue.
Conclusion for How Do Oil Burner Nozzles Work HVAC
Oil burner nozzles play a crucial role in the HVAC system by delivering a precise amount of oil for combustion. Understanding how they work can help optimize heating efficiency and reduce energy costs. By maintaining and replacing these nozzles as needed, homeowners can ensure a comfortable and cost-effective heating experience.